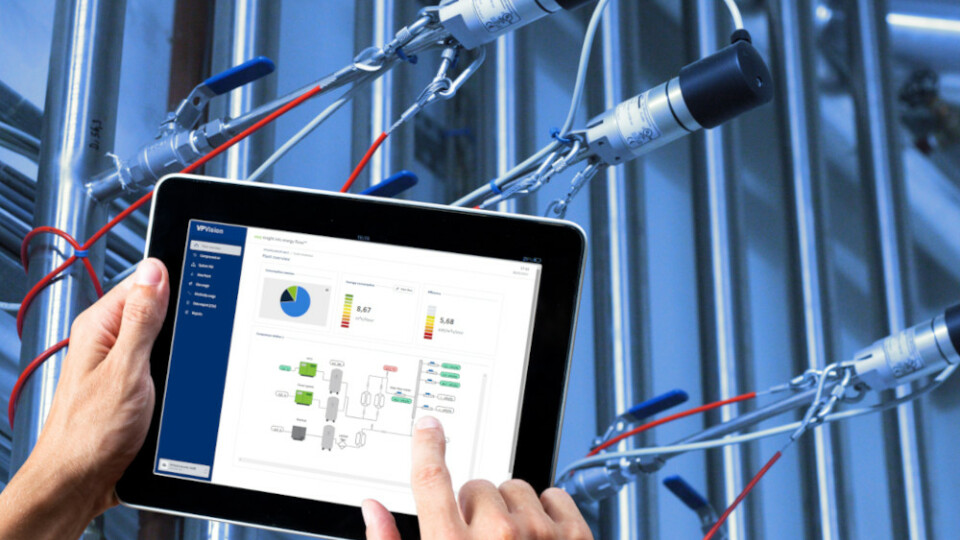
Elektronicafabrikant bespaart ruim 450.000 euro per jaar door monitoring persluchtsysteem
Dankzij de persluchtmetingen in combinatie met monitoring van het energiesysteem bespaart een elektronicafabrikant jaarlijks 455.000 euro op de elektriciteitsrekening.
Perslucht is onmisbaar in de industrie, het is een van de meest gebruikte energiebronnen. Perslucht is goed voor 10 procent tot 30 procent van het totale energieverbruik in de industriële productie, en soms zelfs meer. Perslucht is een van de duurste utilities, en daarom is persluchtefficiëntie bijzonder cruciaal.
Helaas krijgt in veel fabrieken persluchtbesparing onvoldoende aandacht. Er is niet genoeg tijd beschikbaar om consequent te werken aan het verbeteren van de efficiëntie van het persluchtsysteem, en dat begint met een gebrek aan goede ogen en oren in het systeem. Het volgende komt vaak voor:
Er is helemaal geen monitoring systeem/meting.
Wanneer er een monitoring systeem is, bestaat het uit vermogensmeters. Er zijn geen druk- of flowmeters geïnstalleerd. Er is dus geen volledig beeld.
Wanneer er instrumenten aanwezig zijn, en zelfs aangesloten op een algemeen systeem, is er onvoldoende informatie om de acties ter verbetering van de perslucht te verfijnen.
Dit toepassingsartikel laat zien hoe een monitoringsysteem kan helpen om de efficiëntie van het persluchtsysteem te verbeteren.
Praktijkvoorbeeld
Het betreffende bedrijf is een van 's werelds grootste producenten van halfgeleiders en MLED's, gevestigd in Beijing, China. Perslucht wordt hier vooral gebruikt om chips te drogen, materialen in chips/platen in te bedden, printplaten te vervaardigen en chips te koelen tijdens het productieproces. In deze fabriek en in de halfgeleiderindustrie in het algemeen, moet de zuiverheid van perslucht aan de hoogste normen voldoen vanwege de kritische toepassingen. Voor producten van de beste kwaliteit moet de productieomgeving vrij zijn van verontreinigingen en moet de perslucht olievrij zijn.

Het bedrijf is een van 's werelds grootste producenten van halfgeleiders en MLED's, gevestigd in Beijing, China.
Beschrijving van het systeem
Het persluchtsysteem van de fabriek bestaat uit zeven olievrije centrifugaalcompressoren, twee olievrije schroefcompressoren, twee buffertanks van 15m3, vier droogmiddelen en filtratie. Het systeem is gebouwd in één compressorruimte in de elektriciteitscentrale, met natuurlijke luchttoevoer via ramen. De totale luchtbehoefte aan de vraagzijde bedraagt ongeveer 640m3/min.
Er was geen energie monitoringsysteem aanwezig. Het bedrijf had de beschikking over enkele flow- en druksensoren. De levensduur van deze sensoren was meer dan 10 jaar, en ze waren niet in gebruik. De meetgegevens waren dus onbetrouwbaar.
De fabriek verbruikte elke dag veel perslucht en het eiste tot 20 procent van het totale energieverbruik op. De jaarlijkse kosten voor het persluchtsysteem liepen op tot 2,6 miljoen euro. Noodzakelijk dus, om de persluchtefficiëntie in de fabriek te verbeteren.
Nieuw persluchtmanagementsysteem
In de hele fabriek werd een nieuw persluchtmeet- en monitoringsysteem geïmplementeerd met:
Tien stuks VPFlowScope Probe 4-in-1 om de massaflow, de druk, de temperatuur en de totale flow te meten. Zeven werden geïnstalleerd op de hoofdleidingen naar verschillende afdelingen, terwijl de andere drie op machineniveau werden geplaatst.
Eén dauwpuntsensor werd geïnstalleerd achter de drogers.
Een energie monitoringsysteem om alle realtime meetgegevens te verzamelen, te analyseren, rapporten te genereren en de uitvoering van een energiebesparingsproject te begeleiden.
Bevindingen en oplossingen
De analyse van alle verzamelde meetgegevens leidde tot de volgende diagnoses. De gegevens hielpen dus om op feiten gebaseerde beslissingen te nemen over hoe het systeem kon worden verbeterd. En situatiemonitoring voor en na hielp vast te stellen welke besparingen uiteindelijk werden gerealiseerd.
De omgevingsomstandigheden in de compressorruimte kunnen de efficiëntie van de compressoren beïnvloeden, vooral in het geval van centrifugale compressoren. In deze fabriek ging de inlaatlucht door een eenvoudig vliesfiltersysteem, dat gemakkelijk verstopt raakte. Dit resulteerde in een grote onderdrukwaarde in het luchtcompressorstation. Hoewel de filters wekelijks werden vervangen, lag de onderdrukwaarde tussen -30Pa en -40Pa. Hoe langer de filtervervangingscyclus, hoe groter de negatieve drukwaarde. Door de slechte ventilatie overschreed de kamertemperatuur ook het toegestane bereik voor de werking van de apparatuur. Het is bewezen dat wanneer de luchttemperatuur bij de inlaat van de compressor met 3°C daalt, het uitlaatvolume met 1 procent toeneemt.

De omgevingsomstandigheden in de compressorruimte kunnen de efficiëntie van de compressoren beïnvloeden.
Ter verbetering van de ventilatie van het luchtcompressorstation werden tien vliesfilters van 1x2m aan de zijwand van de ruimte toegevoegd om de toevoer van verse lucht te vergroten. Daardoor steeg de onderdruk in de ruimte tot -10Pa. De temperatuur aan de westkant van het luchtcompressorstation werd met ongeveer 1°C verlaagd, en de temperatuur aan de oostkant zelfs met 6-8°C, waardoor de bedrijfsomstandigheden van de luchtcompressoren en drogers sterk verbeterden.
Elke bar lagere druk bespaart 7 procent energie
De totale systeemdruk was onredelijk hoog ingesteld op 7 bar, omdat niet alle afdelingen dit drukniveau nodig hadden om te kunnen functioneren. Het kost meer energie om deze druk in de hele fabriek te handhaven. Een totale systeemdruk van 6 bar bleek voldoende te zijn. Alleen door deze verbetering bespaarde de fabriek al 7 procent op de energierekening.

Elke bar lagere druk bespaart 1 procent energie.
Voldoende buffervolume toevoegen om de compressor beter te regelen
Het volume van de buffertank was te klein, en de systeemdruk fluctueerde aanzienlijk (meer dan 0,5 bar). Wanneer de systeemdruk onder of gelijk was aan 7,0 bar, werd automatisch een koude stand-by-compressor gestart, gelost en kort daarna gestopt. Dit resulteerde in extra stroomverbruik zonder enig effect op het persluchtverbruik. Twee buffertanks, 12m3 en 15m3, werden toegevoegd om de buffercapaciteit te vergroten. Hierdoor werd de fluctuatie teruggebracht tot ongeveer 0,2 bar. In combinatie met de algemene drukverlaging werd het onnodig in werking stellen van de koude stand-by compressor voorkomen.

Het toevoegen van een buffertank zal de drukschommelingscurve helpen verlichten.
Er werd een dauwpuntsensor aan het systeem toegevoegd, dicht bij de vraagzijde van de fabriek. Hieruit bleek dat het dauwpunt in de winter zeer laag was. De gegevens ondersteunden de omschakeling van een op tijd gebaseerde regeling naar een regeling op basis van het dauwpunt. Wanneer het dauwpunt -70°C is, worden de droogtorens geactiveerd. De elektrische energie en het voor de regeneratiecyclus benodigde regeneratiegas werden verminderd. De bedrijfsmodus van de droger werd uitgebreid van 8 tot 12 uur.

VPInstruments Dauwpuntsensor biedt nauwkeurige dauwpuntmeting van fabrieksleidingen.
Conclusies
Via experimenten hebben de metingen in combinatie met het energie monitoringsysteem bewezen een krachtig middel te zijn om de energie-efficiëntie in de fabrieken te verbeteren.
Dankzij de gegevens van het persluchtsysteem monitoring konden de specialisten een diepgaande diagnose stellen. De meetgegevens worden rechtstreeks naar de cloud gestuurd en zijn altijd en overal toegankelijk. Industrie 4.0 gebeurt en monitoring verbetert op afstand de efficiëntie van het energiebeheer in alle opzichten.
Er werden verschillende energiebesparende oplossingen genomen om de energie-efficiëntie van de fabriek te verbeteren. Na elke energiebesparende actie gaven de realtimegegevens bewijsmateriaal, waardoor de ingenieurs de gegevens konden analyseren en meer oplossingen konden uitvoeren om energie te besparen.
Door alle verbeteringen steeg de energiebesparing in de fabriek met 13%. Het bedrijf bespaart jaarlijks ongeveer 455.000 euro op de elektriciteitsrekening.

Industrie 4.0 gebeurt en op afstand monitoring verbetert de efficiëntie van het energiebeheer in alle opzichten
Bron: Compressor Technology.